عیوب در جوشکاری برسی روي هم افتادگي (انباشتگي جوش در کنارهها) overlap or over - roll نقصي در کنار يا ريشه جوش که به علت جاري شدن فلز بر ري سطح فلز پايه ايجاد مي شود بدون اينکه ذوب و جوش خوردن با آن ايجاد شود. علت 1. سرطان حرکت کمتر از حالت نرمال يا طبيعي 2. زاويه نادرست الکترود 3. استفاده از الکترود با قطر بالا 4. آمپراژ خيلي کم نتيجه عوامل فوق کاري مانند بريدگي کناره دارد و يک منطقه تمرکز تنش از فلز جوش ترکيب نشده ايجاد ميکند. سوختگي يا بريدگي کناره جوش Underecut شياري در کنار يا لبه جوش که بر سطح جوش و يا بر فلز جوشي که قبلا را سبب شده است قرار دارد. علت 1. آمپر زياد 2. طول قوس زياد 3. حرکت موجي زياد الکترود 4. سرعت بسيار زياد حرکت جوشکاري 5. زاويه الکترود خيلي به سطح اتصال متمايل بوده است. 6. سرباره با ويسکوزيته زياد نتيجه عوامل فوق موجب يک منطقه تمرکز و يک منطقه مستعد براي ايجاد ترک خستگي ميشود. آخالهاي سربارهSlag inclusion به هر ماده غير فلزي که در يک اتصال جوش بوجود ميآيد آخالهاي سرباره ميگويند؛ اين آخالها ميتوانند در رسوب جوش نقاط ضعيفي ايجاد کنند. علت 1. پاک نشدن مناسب سرباره از پاسهاي قبلي 2. آمپراژ ناکافي 3. زاويه يا اندازه الکترود نادرست 4. آماده سازي غلط نتيجه آخالهاي سرباره استحکام سطح مقطع جوش را کاهش ميدهند و يک منطقه مستعد ترک ايجاد ميکنند. ذوب ناقص L.O.F Lack of fusion عدم اتصال بين فلز جوش و فلز پايه يا بين پاسهاي جوش علت 1. استفاده از الکترودهاي کوچک براي فولاد ضخيم و سرد 2. آمپراژ ناکافي 3. زاويه الکترود نامناسب 4. رعت حرکت بسيار زياد 5. سطح کثيف (پوسته نورد ، لکه ، روغن و ...) نتيجه اتصال جوش را ضعيف ميماند و به يک منطقه مستعد ايجاد خستگي تبديل ميشود. تخلخل Porosity تخلخل سوارخ يا حفرهاي است که به صورت داخلي يا خارجي در جوش ديده ميشود. تخلخل ميتواند از الکترود مرطوب ، الکترود روکش شکسته يا از ناخالصي روي فلز پايه ايجاد شود. همچنين به نامهاي (مک لولهاي) ، (مک سطحي) و (سوراخهاي کرمي) نيز شناخته ميشود. ساير علتها 1. سطح فلز پايه آلوده مثل آلودگيهاي روغن ، غبار ، لکه يا زنگار 2. مرطوب بودن روکش الکترود 3. محافظت گازي ناکافي قوس 4. فلزات پايه با مقادير بالاي گوگرد و فسفر نتيجه به شدت استحکام اتصال جوش شده را کاهش ميدهد. تخلخل سطحي به اتمسفر خورنده اجازه ميدهد که فلز جوش را مورد حمله قرار دهد و موجب نقص در آن شود. همراستا نبودن اتصال جوش Join misagnment اين مشکل معمولا همراستا و همسطح نبودن قطعاتي که به هم جوش ميشوند ناميده ميشوند. عدم همراستايي يک مشکل معمول در آماده سازي روشهاي لب به لب است و هنگامي ايجاد ميشود که صفحات ريشه و صفحات اتصال از فلز پايه در محل درست خود براي جوشکاري قرار نگرفتهاند. علت 1. مونتاژ نادرست قطعاتي که بايد جوش شوند. 2. خال جوشهاي ناکافي که ميشکند يا بست زدن ناکافي که موجب حرکت ميشود. نتيجه همراستا بودن جدي است، زيرا نقص در ذوب لبه ريشه موجب ايجاد مناطق تمرکز تنش ميشود در سرويس دهي موجب شکست خستگي زود رس اتصال ميشود. نفوذ ناقص L.O.P Lack of pentertation عدم نفوذ کامل فلز جوش به ريشه اتصال علت 1. آمپر بسيار پائين 2. فاصله ريشه ناکافي 3. استفاده از الکترود با قطر بالا 4. سرعت حرکت زياد نتيجه سرعت جوش را ضعيف ميکند و به مستعد ايجاد خستگي تبديل ميشود. ترک جوش Weld cracking انواع مختلفي از عدم اتصال ممکن است در جوش يا مناطقي که تحت تأثير حرارت قرار ميگيرند، رخ دهد. جوشها ممکن است داراي تخلخل ، آخالهاي سرباره يا انواع ترکها باشند. تخلخل و آخالهاي سرباره شايد در جوش تا حدي قابل قبول باشد اما ترکها در جوش هرگز قابل قبول نميباشند. وجود ترک در جوش يا در مجاورت جوش نشانگر اين مسئله ميباشد که حتما مشکلي در حين کار وجود داشته است. بررسي دقيق ترکها ، تعيين علت اجاد آنها و نيز راههاي جلوگيري از آنها را براي ما امکان پذير ميسازد. در ابتدا ما بايد به اين مسئله توجه داشته باشيم که بين ترک و شکست تفاوت قائل شويم. منظور ما از ترک ، پديدهاي است که در اثر عواملي مانند انجماد ، سرد شدن و تنشهاي داخلي که به علت انقباض جوش ميباشد ايجاد ميگردد. ترکهاي گرم ، ترکهايي ميباشند که در دماهاي بالا رخ ميدهند و معمولا به انجماد ربط دارند.ترکهاي سرد ترکهايي هستند که بعد از اينکه جوش به دماي اطاق رسيد، رخ دهد و ممکن است حتي به HAZ رابط داشته باشد. بيشتر ترکها در اثر تنشهاي فيزيکي انقباض که معمولا با کشيدن يا تغيير شکل جسم همراهي باشد در هنگام سرد شدن جوش رخ ميدهد، ايجاد ميشوند، اگر انقباض محدود شود، اين تنشهاي فيزيکي کرنشي ، تنش داخلي پسماند را بوجود ميآورند که اين تنهاي پسماند منجر به ايجاد ترک ميشوند. در واقع دو نيروي مخالف وجود دارد: 1. تنشي که بوسيله انقباض ايجاد ميشود. 2. استحکام و سختي فلز پايه تنشهاي ناشي از انقباض با افزايش حجم فلزي که تحت انقباض قرار گرفته است، افزايش مييابد. جوشهايي در ابعاد بزرگ و فرآيندهايي با نفوذ زياد کرنشهاي انقباضي را افزايش ميدهند. تنشهايي که در اثر کرنشهاي انقباضي ايجاد ميشود با افزايش استحکام فلز پر کننده و فلز پايه افزايش مييابد. همچنين وقتي که استحکام تسليم افزايش بايد تنش پسماند نيز افزايش مي يابد. 1. ضرورت جوشکاري 2. پيشگرم 3. دماي بين پالسي 4. عمليات حرارتي پس از جوش 5. طراحي اتصال 6. روشهاي جوشکاري 7. مواد پر کننده ترک به صورت خط مرکزي ترک به صورت خط مرکزي در مرکز يک پاس جوش معين قرار دارد. اگر انتهايي کپاس جوش داشته باشيم و اينپاليدرمرکز اتصال باشد آنگاه اين ترکمرکزي در مرکزاتصال نيز رار خواهد داشت. در مورد پاس هاي چند تاي که چندين پاس در هر لايه وجود دارد ترک مرکزي از نظر هندسيب ممکن است در مرکز اتصال قرار نداشته باشد. ار چه اغلب ديده مي شود که در مرکزاتصال قرار دارد. علت ترک مرکزي يکي از سه پديده زير مي باشد: 1. ترکي که ناشي از جدايش و تفکيک باشد. 2. ترکي که مربوط به شکل گرده جوش ميباشد. 3. ترکي که مربوط به تغييرات سطحي ميباشد. متأسفانه تمام سه پديده فوق خودشان را در قالب يک نوع آشکار ميکنند و تشخيص دادن ترک مشکل ميباشد. علاوه بر اين ، تجربهها نشان دادهاند که اغلب 2 يا حتي 3 پديده فوق با يکديگر برهمکنش داده و در ايجاد ترک مؤثرند. در واقع درک مکانيسم اصلي هر يک از انواع ترکهاي مرکزي به ما کمک ميکنند تا به دنبال راه حلي براي از بين بردن ترک باشيم. ترک مرکزي ناشي از جدايش اين ترکها وقتي رخ ميدهد که ترکيباتي با نقطه ذوب پايين نظير فسفر ، روي ، مس و گوگرد در نقاط خاصي در حين فرآيند سرد شدن جدايش يابند. در حين فرآيند انجماد ، ترکيباتي با نقطه ذوب پايين در فلز مذاب به نواحي مرکزي اتصال رانده ميشود چون آنها تا آخرين ترکيباتي هستند که شروع به انجماد ميکنند و جوش در اين نواحي تمايل به تفکيک و جدايش مييابد. در جوشکاري ميتوان از الکترودهايي با مقادير بالاي منگنز استفاده تا بتوانيم بر تشکيل سولفيد آهن با نقطه ذوب پايين غلبه کنيم. متأسفانه اين مفهوم نميتواند براي مواد غير فرار ديگري بجز گوگرد بکار رود. ترک مرکزي ناشي از شکل گرده جوش نوع دوم ترک مرکزي ترک ايجاد شده در اثر شکل پالس جوش ميباشد، اين ترک در فرآيندهايي که همراه با نفوذ عميق ميباشند نظير فرآيند FCAW , SAWتحت محافظ CO2 ديده ميشود. وقتي که يک پالس جوشکاري داراي عمق بيشتري نسبت به هضم آن جوش (در نماي سطح مقطع) باشد. براي رفع اين نوع ترک ، پالسهاي جوش بايد داراي عرضي حداقل برابر با عمق باشد. توصيه ميشود که نسبت پهناي جوش به عمق آن برابر با 1 به 14/1 به 1 باشد تا اين نوع ترک رفع شود. اگر از پالسهاي چندتايي استفاده شود هر پاس داراي پهناي نبت به عمق آن باشد، يک جوش فاقد ترک خواهيم داشت. وقتي که يک ترک مرکزي بخار شکل پاس تحت بررسي است، تنها راه حل اين است که نسبت پهناي جوش به عمق آنرا تغيير دهيم. اين موضوع شايد در برگيرنده آن باشد که تغييري در طراحي اتصالها داشته باشيم. از آنجايي که عمق جوش تابعي از نفوذ ميباشد شايد مفيد باشد که مقدار نفوذ را کاهش دهيم بدين منظور ميتوانيم از آمپرهاي پايينتر و الکترودهايي با قطرهاي بالاتر استفاده کنيم. راهکارهاي فوق دانسيته جريان را کاهش ميدهد و مقدار نفوذ را محدود ميکند. ترک مرکزي ناشي از شرايط سطحي جوش آخرين مکانيسمي که سبب ايجاد ترک مرکزي ميباشد تغيير شرايط سطحي ميباشد. وقتي جوشهايي با سطح مقعر ايجاد ميشود تنشهاي ناشي از انقباضهاي داخلي موجب ميشود که سطح جوش کشيده شود. برعکس وقتي که سطح جوش محدب باشد نيروي ناشي از انقباضهاي دروني موجب ميشود که سطح جوش فشرده ميشود. سطح جوش مقعر ، اغلب ناشي از ولتاژهاي بالاي قوس ميباشد. کمي کاهش در ولتاژ قوس موجب ميشود که گرده جوش به حالت محدب تغيير شکل دهد و تمايل به ترک حذف گردد. سرعتهاي حرکت بالا نيز ممکن است به اين موضوع کمک کند و کاهش در سرعت حرکت جوشکاري ، مقدار پراکندگي توسط جوش را افزايش ميدهد و سطح جوش به صورت محدب تغيير حالت ميدهد. جوشکاري در حالت قائم سر پايين باعث ايجاد اين نوع ترک ميشود. جوشکاري در حالت قائم رو به بالا ميتواند از بروز اين نوع ترک جلوگيري نمايد. ترک منطقه متأثر از جوش ترک منطقه متاثر از جوش HAZ بوسيله جدايشي که بلافاصله مجاور گرده جوش رخ ميدهد مشخص ميشود، اگر چه اين نوع ترک مربوط به فرآيند جوشکاري ميباشد با اين حال ترکي است که در روي پايه رخ ميدهد نه درخود جوش. اين ترک به نام تک مجاور جوش ، ترک گوشهاي يا ترک تأخيري نيز ناميده ميشود. چون اين ترک بعد از اينکه فولاد در دماي f ْ400 انجماد يافته است رخ ميدهد ترک انجمادي نيز ناميده ميشود و چون با هيدروژن نيز همراه ميباشد ترک همراه با هيدروژن نيز ناميده ميشود. براي اينکه ترک HAZ رخ دهد سه شرط بايد بطور همزمان برقرار باشد: 1. بايد مقدار کافي هيدروژن وجود داشته باشد. 2. جوش بايد به حد کافي نفوذ پذير باشد. 3. بايد به حد کافي تنشهاي داخلي يا پسماند وجود داشته باشد.حذف يکي از سه شرط فوق معمولا باعث ميشود که اين نوع ترک از بين برود. در جوشکاري ، يک راه براي حذف اين نوع ترک اين است که دو يا سه متغير (مقدار جوش نفوذ پذير جوش) را محدود کنيم. هيدروژن از منابع مختلفي ميتواند وارد جوش شد. رطوبت و ترکيبات آلي منابع اصلي هيدروژن در جوش ميباشند. هيدروژن ميتواند در فولاد ، الکترود ، ترکييبات روپوش الکترود و در آتمسفر وجود داشته باشد. ترک عرضي ترک عرضي ترک متقاطع نيز ناميده ميشود. ترکي است که در جهت عمود بر طول جوش ايجاد ميشود. اين نوع ترک از انواعي است که اغلب در جوشکاري با آن مواجه ميشويم و معمولا جوشي که داراي استحکام بالاتري در مقايسه با فلز پايه ميباشد ديده ميشود. اين نوع ترک ميتواند همراه با هيدروژن نيز باشد و کل ترک منطقه متأثر از جوش HAZ که پيشتر شرح داده شد ناشي از مقدار بالاي هيدروژن ، تنشهاي پسماند و ريز ساختارهاي حساس ميباشد. فرق عمده بين اين دو ترک اين ميباشد که ترک عرضي در فلز جوش نتيجه تنش پسماند طولي ميباشد. چنانچه پاس جوشکاري بصورت طولي انقباض يابد، فلز پايه در مقابل اين نيرو مقاومت ميکند و در واقع دچار تراکم و فشردگي ميشود. استحکام بالاي فلز پايهاي که در مجاورت جوش ميباشد در برابر فشردگي ناشي از انقباض جوش مقاومت ميکند و در واقع فشرده شدن جوش را محدود ميکند. بخاطر ممانعتي که فلز پايه به عمل ميآورد، تنشهاي طولي در جوش گسترش مييابد.وقتي با ترکهاي عرضي مواجه ميشويم بايد سطح هيدروژن و شرايط نگهداري الکترودها را مد نظر داشته باشيم. در مورد ترک عرضي ، کاهش استحکام فلز جوش معمولا يکي از راهکارهاي حذف اين نوع ترک ميباشد. تأکيد زيادي بر روي فلز جوش وجود دارد چون فلز پر کننده به تنهايي ممکن است جوشي رسوب دهد که داراي استحکام پايينتري باشد و نيز تحت شرايط عادي فلزي نرم باشد. البته با تأثير عناصر آلياژي استحکام جوش بالا ميرود و از نرمي آن کاسته ميشود. استفاده از جوشهايي با استحکام پايينتر ، يک راه حل مؤثر در کاهش ترک عرضي مؤثر ميباشد، البته به شريطي که استحکام جوش با استانداردهاي تعريف شده مطابقت داشته باشد. پيچيدگي پيچيدگي يا اعوجاج تا حدي در تمام انواع جوشکاري وجود دارد، در بسياري موارد آنقدر کوچک است که به سختي قابل رؤيت است، ولي در بعضي موارد بايد پيش از جوشکاري به اعوجاجي که متعاقبا ايجاد ميشود توجه کرد. مطالعه و بررسي اعوجاج بسيار پيچيده است و آنچه در ادامه آمده خلاصه است: علل اعوجاج هنگامي که فلز تحت بار ، کرنش ميکند يا حرکت ميکند و تغيير شکل ميدهد: تحت بار گذاري ضعيف فلزات بصورت الاستيک باقي ميمانند. (به شکل اصلي خود باز ميگردند يا پس از اينکه بار برداشته شد شکل ميگيرند) که اين تحت عنوان محدوده الاستيک شناخته ميشود. تحت بار خيلي زياد ، فلزات تا حدي تحت تنش قرار ميگيرند که ديگر به شکل اول خود باز نميگردند يا شکل نميگيرند و اين نقطه (نقطه تسليم) ناميده ميشود (تنش تسليم).فلزات با حرارت ديدن انبساط مييابند و وقتي سرد ميشوند منقبض ميشوند، فلزات در حين جوشکاري گرم و سرد ميشوند که موجب تنشهاي بالاي ناگهاني و اعوجاج ميشوند. اگر اين تنشهاي زياد از محدوده الاستيک بگذرند و از نقطه تسليم نيز رد شوند، برخي پيچيدگيهاي دائمي در فلز پديد ميآيد، تنش فلز در دماي بالا کاهش مييابد. اعوجاج اثر ناخواسته انبساط و انقباض فلز حرارت ديده است. انواع پيچيدگي سه نوع اصلي پيچيدگي وجود دارد: 1. زاويهاي 2. طولي 3. عرضي کنترل پيچيدگي ميتواند در سه مرحله انجام گيرد: * قبل از جوشکاري * حين جوشکاري * بعد از جوشکاري کنترل پيچيدگي قبل از جوشکاري توسط روشهاي زير انجام ميشود: 1. خال جوش زدن 2. گيره ، بست و نگهدارنده 3. پيشگرم کامل و سرتاسري 4. مونتاژ اوليه مناسب کنترل اعوجاج پس از جوشکاري: 1. سرد کردن آرام 2. صافکاري شعلهاي (حرارت دهي معکوس) 3. آنيل کردن 4. تنش زدايي 5. نرمال کردن 6. صافکاري مکانيکي در سازههاي فلزي ساختمان معمولا روشهاي 1و2 بيشتر اعمال ميگردد و ساير روشها در کارهاي صنعتي بيشتر کاربرد دارند. آنيل کردن يک پروسه عمليات حرارت است که براي نرم کردن فلزات جهت کل سرد يا ماشين کاري بکار ميرود، قطعه يا کار نهائي معمولا در کوره تا دماي بحراني (براي فولاد با 0.52% کربن حدود Cْ 820 - 723) حرارت داده ميشود و سپس به آرامي سرد ميشود. تنش زدائي حرارت دهي يکنواخت قطعات جوش شده تا دمايي زير دماي بحراني است که با سرد کردن آرام دنبال ميشود، اين پروسه نقطه تسليم فلز را کاهش ميدهد، لذا تنشهاي باقي مانده در قطعه کاهش مييابد. نرمال کردن پروسهاي براي ريز کردن ساختار دانهاي فلز است که موجب بهبود مقاومت آن در برابر شوک و خستگي ميشود. در نرمال کردن قطعات جوش شده تا بالاي دماي بحراني (Cْ 820 براي فولاد با کربن 0.25% (تقريبا يک ساعت براي هر nm 25 ضخامت حرارت ميبيند و سپس در هوا سرد ميشود (مستقيم کاري).
ارسال نظر برای این مطلب
درباره ما
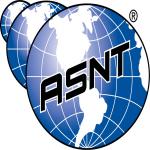
سلام به وبلاگ بنده خوش آمدید از دوستانی که مایل به آموزش و یا در یافت مدارک بازرسی جوش ASNT و یا انواع مدارک در ضمینه جوشکاری و انجام جوشکاری اغتشاشی می باشند لطفا به شماره بنده تماس حاصل فرماید. با تشکر مدیریت شرکت پیشرو ناظران - قدمی 09179147053
اطلاعات کاربری
لینک دوستان
پیوندهای روزانه
آمار سایت
کدهای اختصاصی
اموزش بازرسی جوش در شیراز ، صدور مدارک بازرسی جوش ASNT ،صدور مدارک جوشکاری ،مدارک ASNT در شیراز